Structural interlayers in laminated glass have allowed engineers and specifiers to extend and improve the use of glazing solutions in the construction industry. With the availability of embodied carbon values for these interlayers, it is now possible to assess more accurately the reduction in environmental footprint of laminated glass for construction projects. The Tour Montparnasse tower refurbishment project in Paris was selected as a case study to make a comparison between PVB and structural ionomers in terms of embodied carbon. A 15 % embodied carbon reduction could be achieved using the structural interlayer.
There are many contributors to a building’s carbon footprint, some obvious, and some that aren’t quite so obvious. The building’s energy use is something that almost everyone is aware of, and efforts to reduce that with solar, wind, or geothermal elements are fairly common. Water supply is another contributing factor, as pumping it to the building requires fossil fuels. Some lesser-known factors are the greenhouse gas emissions caused by the transportation of materials to the job site, as well as the embodied carbon of those materials used to construct the building. home glass decors
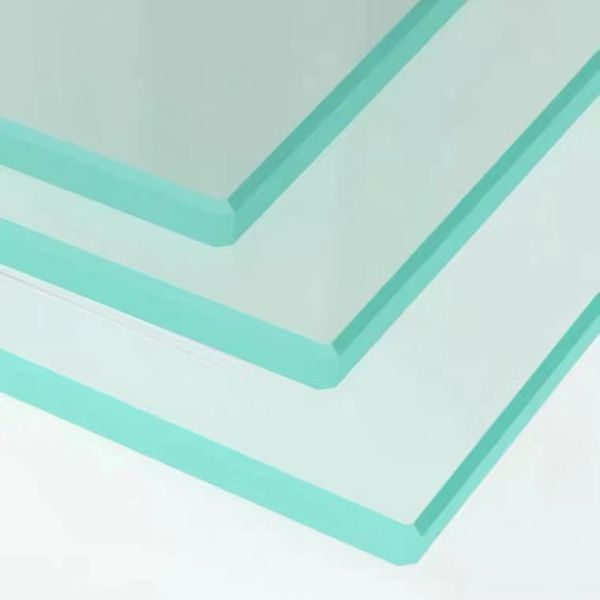
The amount of glazed surface in a building has steadily been increasing during the past decades. Natural lighting, comfort and transparency needs have been driving that trend. But the mass of glass per square meter of glazed surface has also increased due to a combination of energy, comfort, structural, security and safety requirements. The specification of double and triple glazed unit as well as laminated glass are a good illustration of that trend.
The majority of the laminated glass specified is made out of PVB interlayers with a relatively low coupling value. This has a negative impact on the total glass thickness needed to meet the stress and deformation requirements. That was the reason for the introduction of structural interlayers which allowed engineers and specifiers to design with thinner laminated glass constructions. At first, theobjectives were to increased glass sizes, reduce glass weight and therefore supporting structure and improve post-breakage performance, especially for toughened laminated glass.
But with the growing sustainability challenges which is driving the selection of construction materials towards products with lower embodied carbon, the reduction of glass thickness through the use of structural interlayers can contribute to that goal.
To establish the environmental footprint of construction materials, a life cycle assessment (LCA) is performed. One of the indicators calculate during this process is the global warming potential (GWP) in Kg CO2 equivalent. This value is also often described as the carbon footprint of the material.
Embodied carbon values are now available for traditional PVB and Structural ionomers. Embodied carbon values can vary from supplier to supplier and depending on the manufacturing site and process.
In this paper, the interlayer embodied carbon values provided by Kuraray are used. The system followed is “cradle to gate”. The LCA calculation was done according to ISO 14040 and ISO 14044 and with the GaBi Software based on the GaBi2022.1 database (DB) from Sphera®.
The authors have chosen to illustrate the differences in embodied carbon through a façade refurbishment project in Paris: The Montparnasse Tower.
2.1. Presentation of the project and its double skin façade
The Montparnasse Tower in Paris, originally built between 1969 and 1973 is currently under a major refurbishment, including the replacement of the 40 000m² of the existing façade to improve the environmental performance of the building. The refurbishment project, designed by the architecture firm “Nouvelle AOM”, defines six principal typologies for the façades (see Fig. 1).
In this kind of project, the façade represents a big part of the carbon footprint, around 30% in this case,so every identified lever to reduce the carbon footprint of the facades has a consequent impact on the whole project.
The checkerboard façade is the biggest typology on the new project, representing 27 000m². It will be a natural ventilated double skin façade assembled in a unitised system. Each unit is approximatively 5,7m wide by 3,15m high. The deepness of the double skin varies between 600 mm and 900 mm. The outer skin is composed of one laminated glass panel and the inner skin is composed of 4 IGU panels. (See Fig. 2). All glasses are annealed.
2.2. Design of the outer glass
The design of the new façade presented a big challenge, in special for the additional weight compared to the existing one. The main core of the tower is supported by prestressed concrete beams spanning above the subway station, so it was critical to limit the impact on the load takedown.
Reducing the weight of the facades is also a double lever to limit the carbon footprint of the project. The lighter the façade, the less embodied carbon on it, but also the less of structural reinforcements needed.
As the main design load for the façade is the wind load, wind tunnel tests have been carried to precisely establish the wind load on the façades. The wind tunnel test, combined with the use of a structural interlayer have allowed to minimize the thickness of the laminated glass. The specified structural interlayer is SG-5000.
The laminated glass of the outer skin of the checkerboard façade has been calculated according to the equivalent thickness method defined in EN 16612 and the DTA (French technical approval) of the SentryGlas®.
A comparative with a standard PVB interlayer has been also established. This allowed the design team to evaluate the advantages of using the structural interlayer (See Fig. 3).
Following the thickness calculations, the carbon footprint of both options has been established. According to the National French INIES database (this database is established according to NF EN 15804), the kgCO2eq/m² for each glass composition has been defined. The impact of the interlayer in the LCA is integrated according to the information provided by Kuraray. The thickness of the interlayer considered in the calculations is 0.76mm for the PVB and 0.89 for SG-5000 option.
The values considered for each glass compositions are calculated as follows (stages A1-A5 and B1-B7for a life span of 30 years).
Table 1: Values for determining LCA of laminated glass.
The results of the calculation are given in Fig. 4 below.
The use of the structural interlayer allows to reduce by 15% the carbon footprint of the outer glass pane of the checkerboard façade.
It is to be noted that the outer glass represents around 20% of the total carbon footprint of the checkerboard façade when a life span of 50 years is considered.
When selecting the type of laminated glass and interlayer, the engineers and specifiers have now an extra tool to reduce the environmental footprint of the building they are designing.
In the case of the Montparnasse tower, an ionomer structural interlayer allows the reduction of the embodied carbon of the glazing material by 15%.
Embodied carbon values used to get to this result are based on the values available at the moment this paper was written and are evolving constantly.
Database INIES. https://www.base-inies.fr/iniesV4/dist/consultation.html
French approval DTA SentryGlas® 6/15-2253_V2
25F, Huarun Mansion A, 6 Shandong Road, Qingdao, PR China Qingdao Shi Shandong Sheng, 266071 China
Via del Lavoro, 1 22036 Erba CO Italy
Industrial zone RZ R29 51223 Kukuljanovo Croatia
No. 20 Binhe Road, High-tech Development Zone, Luolong Qu Luoyang Shi Henan Sheng, 471003 China
Koroglu Rahimov str.57-57A, AZ1072 Baku Azerbaijan
Pol. Ind. Penapurreira Parcela C4-B, 15320 As Pontes de García Rodríguez A Coruña Spain
2200 W. Salzburg Rd. Auburn , MI 48611 United States
No. 160 Yichuan Rd., Jiaonan Shi Qingdao Shi Shandong Sheng, 266000 China
19, rue du Puits Romain, 8070 Bertrange Luxembourg
İçmeler Mah.D-100 Karayolu Cad.No:44A, 34947 Tuzla, /İstanbul Turkey
3196 Thompson Road Fenton , MI 48430 United States
2300 Harmon Road Auburn Hills , MI 48326 United States
779 Washington Street Buffalo , NY 14203 United States
12 place de l'Iris 92400 Courbevoie France
Via Marcatutto 7, (Milan) Italy 20080 Albairate MI Italy
No. 3 Building Resources Boya Plaza, Xiangling Road Qingdao Shi Shandong Sheng, 266071 China
1860 Air Lane Drive Nashville , TN 37210 United States
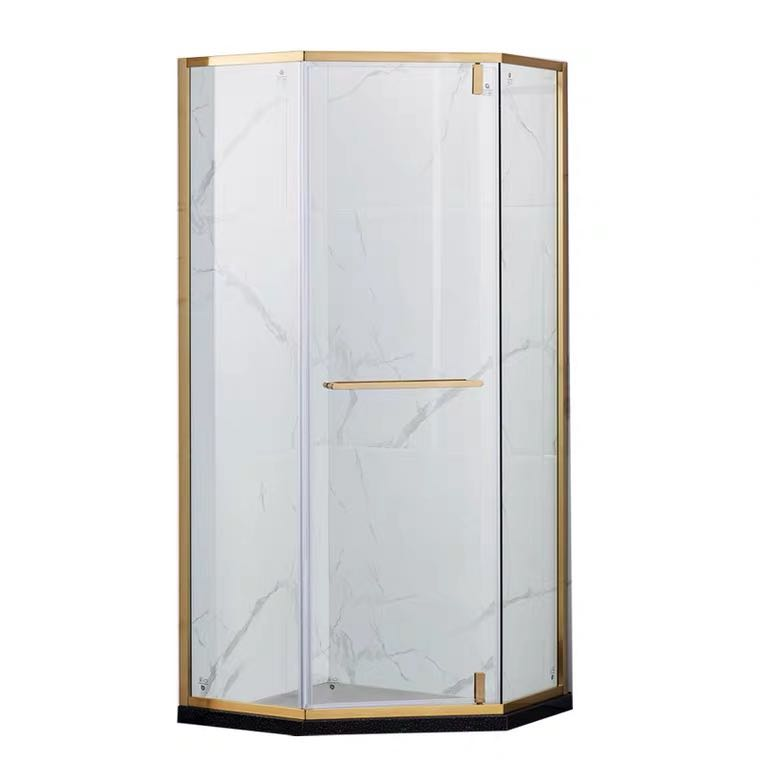
Heat Resistant Glass For Building Log in or register to post comments